滚子是滚动轴承中的重要部件,为了保证滚子的质量,检测是整个滚子生产环节当中非常重要的一环,直接影响着滚子的品质和销量。但是,目前滚子成品外观的检测主要还是依赖人工。目前市场上也会有一部分企业用机器视觉进行缺陷检测,但由于技术限制、稳定性差,误检率基本在20% - 30%左右,无论是对工艺还是对成本来说,这都是巨大的浪费。
深度视觉将机器视觉、计算机图像处理、人工智能等多项前沿科技深度结合,为工业制造企业提供高效智能的视觉检测方案。
本文将对我们所开发的柱状滚子(圆锥滚子、圆柱滚子和球面滚子)检测设备的检测功能和技术研究做分享。
我们研发的滚子外观检测设备,能够满足高节拍的检测需求,自动完成滚子不同区域(包括端面、倒角、外径)的外观缺陷检测,检测内容覆盖了滚子检测中的所有常见缺陷种类。
滚子作为金属件,具有高反光、高曲率的特点,同时在滚子表面还会有清洗油、防锈油等附着。针对这些特点,我们基于自身在光学领域的积累和经验,结合每个检测面的特点以及缺陷种类,进行了针对性的光路设计。每个检测面搭配了一种或多种打光方案,通过不同的光源和照射角度,使得缺陷在图像中能够成像清楚,并和背景对比明显。下图(滚子各部位成像)展示了滚子不同检测面的缺陷成像。
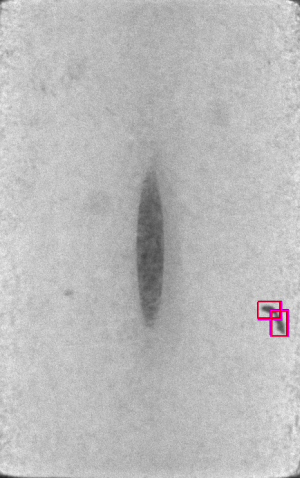
从上面几张图可以看出来,虽然滚子表面由于工况复杂会有脏污、无深度的划痕以及表面的纹路等干扰因素,但是缺陷的成像和以上干扰因素还是有明显的区别,能够准确地将缺陷检测出来。
相较于轴承中常见的套圈、成品轴承,滚子的体积较小,由此决定了滚子的生产节拍要明显高于套圈和成品轴承,其生产节拍最高可以达到每分钟200粒。为了不降低生产节拍,滚子的外观检测设备也必须达到这样的节拍,因此一款合格有效、真正能够为企业解决实际痛点的滚子外观检测设备,必须要解决高速检测的问题。
我们针对滚子的高速检测问题,设计实现了智能相机、传统图像算法和AI算法相结合的多级算法架构:
深度视觉具备智能工业相机(下图)的研发能力,基于自身在轴承行业多年的行业经验,在相机端融入了图像处理、缺陷检测等高速算法。以智能相机为依托,实现了算力分摊,即由相机完成图像处理和常见缺陷检测等算法,大大减少了运行在工控机端的传统图像算法的算力需求;同时智能相机输送给工控机端的不仅仅是经过质量优化的图像,更包含了内置智能算法提取的初级图像特征,有效支持了传统算法的运算。
在缺陷检测中最棘手的问题即为缺乏缺陷样本,有些缺陷对生产厂商来说非常重要、不可漏检,但实际生产中又很少遇到。目前常见的视觉检测厂商,通常是基于深度学习去实现缺陷检测,对于此种没有遇见的缺陷,很容易漏检。
我们为每台视觉检测设备配备了高配置工控机,搭载了自主开发的传统图像检测算法,能够覆盖滚子检测范围内的所有常见缺陷。即使客户暂无法提供缺陷样件,基于我们对滚子生产过程的理解和把握,能够提供相应的缺陷检测算法,保证无漏检。
工控机端的传统算法为了保证缺陷不漏检,会存在一定的误判;同时滚子生产中的复杂工况也会对传统算法的检测准确率造成一定的影响。通常对检测准确率影响最大的干扰因素包括产品表面油的干扰(油泡和油斑等)、产品流转过程中的脏污等。相对于缺陷样本,此类易导致误判的干扰样本可以比较容易的收集,我们充分利用了AI算法在特征提取和适应性方面的优势,将AI算法应用到干扰因素的过滤上,即相机端和工控机端检出的缺陷,会经过AI算法进行再次判定,识别到检出的缺陷实际是干扰的时候,重新认定该产品为合格产品。这样的机制下,可以有效提高视觉检测设备的一次通过率,降低滚子生产企业的成本。
深度视觉的滚子外观检测设备,目前已形成高中低端搭配、标准化的系列产品,能够满足不同客户的检测需求,产品检测范围能够覆盖大部分产品型号(如下图所示)。
根据客户的需求深度视觉可以提供包括上下料、外观检测设备、涂油包装等一整套解决方案(如下图所示),目前已在国内外多个知名客户的产线上成功应用,有效提高了客户的生产效率、检测质量,降低了人力成本。
#机器视觉检测系统#